International Graphite is building a multi-faceted downstream processing operation at Collie, incorporating state of the art research and development facilities, to meet global demand for graphite products and maximise the value of its graphite resource.
In a staged development program, the company has achieved significant milestones, including the successful commissioning of a pilot scale micronising and spheroidising plant at Collie – the largest and most advanced facility of its kind known to be operating in Australia.
Plans are now underway to expand to product “qualification scale” equipment which will demonstrate the company’s capacity to produce micronised graphite and provide the quality control necessary to gain customer sales agreements. In March 2023, the Company released the Definitive Feasibility Study for a A$12.5 million graphite micronising facility with a nominal capacity of 4000 tpa. The commercial plant will be one of the first of its kind in Australia and is expected to be operational in 2025.
The Collie facility is also the centre of International Graphite’s research and development program for battery anode material and will use third-party fine flake graphite as feedstock until the company’s Springdale graphite resource comes online. In the future, it is expected that micronised and spheroidised graphite product will be further purified and coated at Collie to produce a finished battery anode material product suitable for the manufacture of lithium-ion battery anodes.
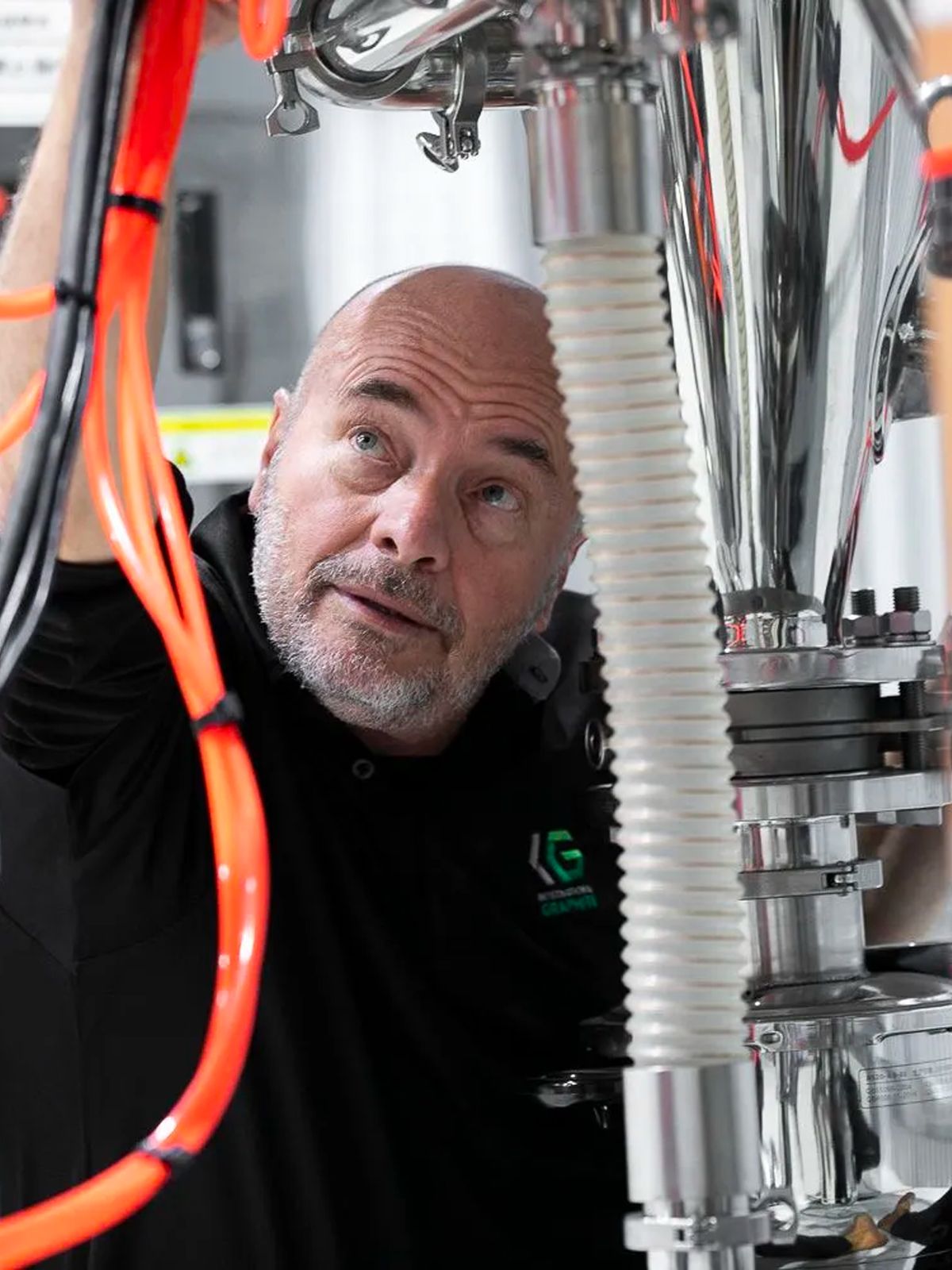
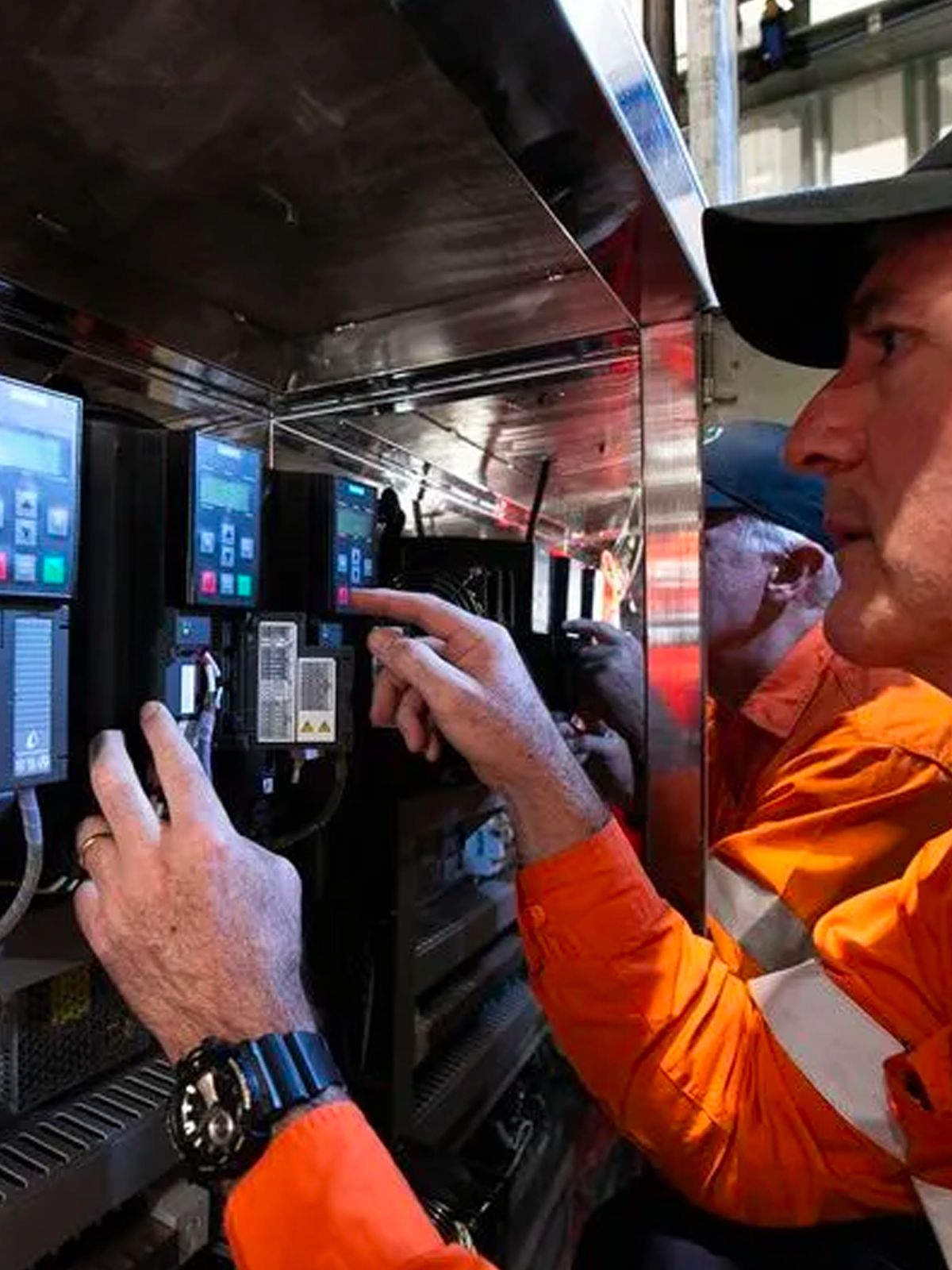
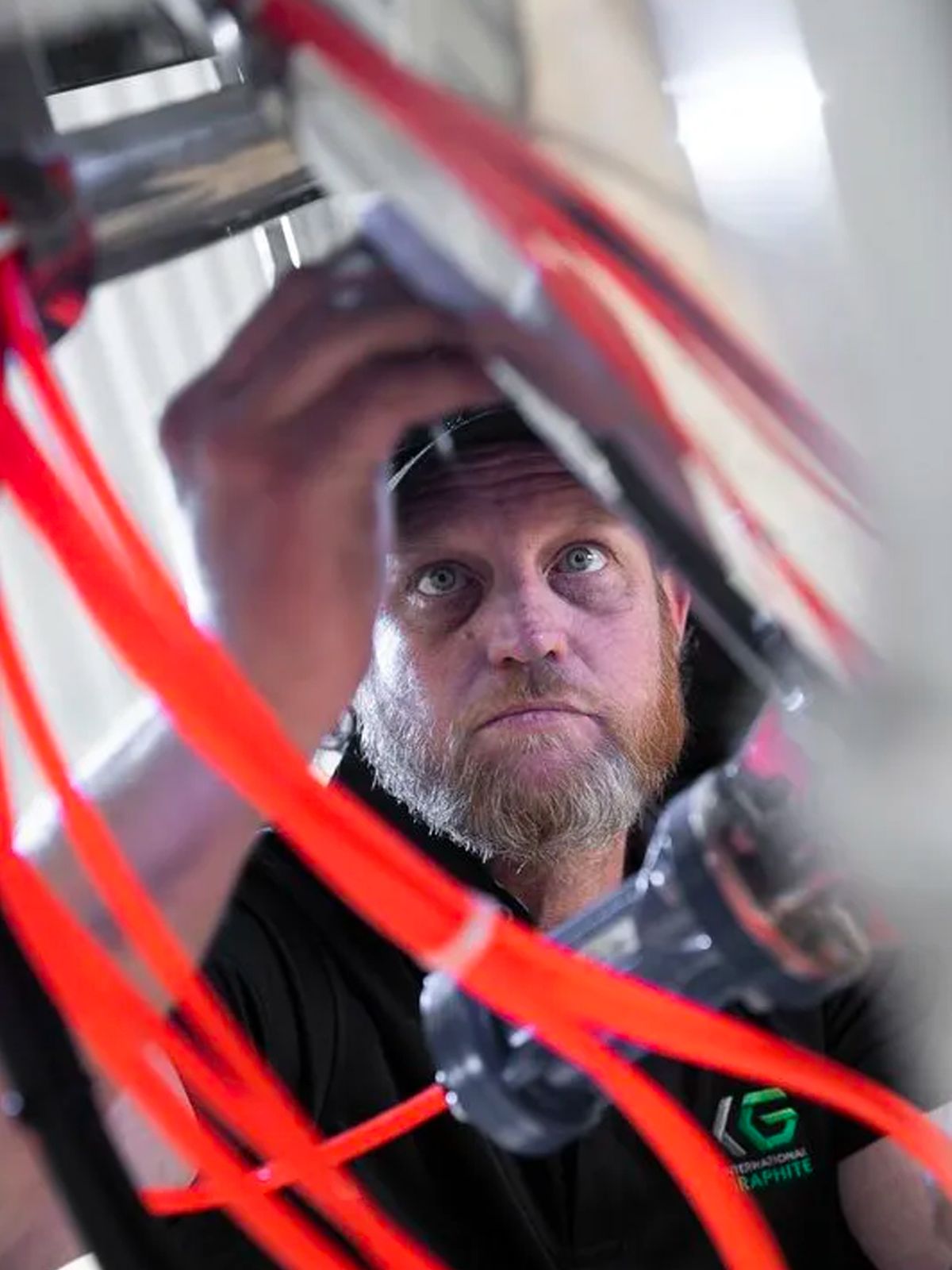

High and Ultra High Purity Micronised Graphite
The first commercial product line at Collie will be a nominal 4000 tpa micronising plant producing ultra-fine micronised graphite as an additive for industrial products. The Collie plant will receive graphite concentrates at 95% and 99% purity to produce micronised graphite at both 95% TGC and 99% TGC in different size fractions. As one of world’s most versatile manufacturing materials, micronised graphite is used for many high-demand industrial applications, such as polymers, lubricants and battery cathodes.
Research and Development
Research and development is underway at Collie to establish a new and environmentally responsive graphite purification process. The company has taken delivery of a speciality high temperature furnace and will be investigating thermal purification as an alternative to traditional alkali or acid based purification methods. The micronised and spheroidised graphite is purified to >99.95% and then coated, turning it into a smooth and highly conductive material suitable for lithium-ion battery anodes.
